(203) 775-1234
Products
Below are just a few of the different product categories we have been involved in over the past century. We are open to any and all industries that would benefit from adoption of our electroforming and electroplating services. We make hardware for government labs, prime defense contractors, commercial companies... we even make parts for the film industry.
​
What can we help you create?
Precision Microwave Hardware
Microwave energy that is transmitted through air or space, must also be transmitted from the antenna to the mechanism that deciphers the information. This can be done with a metal tube called a waveguide that possesses internal dimensions relative to the wavelengths of the radio frequency energy passing through it. The higher the frequency, the smaller the wavelength and the smaller the waveguide dimensions. Also, RF designers put geometric features inside the waveguides that alter the electromagnetic field structure to do what they want it to. These features often require very high precision dimensions. A lot of waveguide hardware is made by assembling extruded tubing, castings, and machined parts, but for many tight tolerance and complex waveguide modules, the only way to achieve the internal dimensions needed is by electroforming. We make a wide variety of microwave assemblies for our customers including millimeter waveguides, filters, orthomode transducers, magic tee’s, diplexers, multiplexers, mode converters, couplers, power dividers/combiners, and horn or dish antennas as seen in the attached photos, and have been doing this for air and space microwave transmission since the 1950’s.

As another example, this photo shows microwave antenna horns for receiving satellite TV on airplanes.

Some microwave applications not only require low loss and high power handing capabilities of waveguide but require the compact size and transverse electromagnetic (TEM) capabilities of coaxial transmission lines. We build rigid "air" coaxial cable assemblies where the center conductor is suspended within the outer shield and have manufactured these types of assemblies for over 40 years.

Coldshields for Infra-Red Detectors and Cameras
Infra-red cameras and detectors are like digital cameras, only the pixel system is sensitive to the infrared spectrum instead of the visible light spectrum; a lower frequency than visible light in the Electromagnetic Spectrum. Also, putting a box around the pixel system (chip), as in a photo camera, does not work because infrared energy, which is heat, comes right through the sides of the box. Also, all high end IR cameras and detectors operate at cryogenic temperatures, so the pixel system, and surrounding items, must be rapidly cooled down to be effective. This is especially true for military applications. We make thin walled metal shells that go over the pixel systems upon which the lenses are mounted called coldshields. Coldshields are thin walled metal parts designed to quickly cool down and are gold plated to reflect IR energy coming in from the sides. The interior surfaces are often treated to absorb IR energy coming through the lens at an angle. The interior surfaces of the coldshields typically have complex geometric shapes with extremely accurate dimensions to achieve the “3 bounce rule” for dissipating any stray IR radiation entering the lens on an angle, so the pixel array only sees what the camera or sensor is aimed at, and is not blurred by stray radiation.
We manufacture coldshields per our customer’s designs and associated requirements. We also possess reflectance measurement capabilities and can provide IR reflectance data of the exterior gold coating and the IR absorbance of the interior coldshield treatments.

Capacitors
We electroform copper on teflon tubes, through a proprietary bonding technique, which are then machined to form capacitors for MRI machines and other applications.

Reflectors
We make reflectors for aircraft landing lights, optical energy transmission and other uses by electroforming nickel on shiny, reusable stainless steel mandrels. We can also put gold on the mandrels first so the reflectors can have highly reflective gold coatings all over the insides without having to gold plate them afterwards.

Heat Shields
Although heat shields are not normally made to high dimensional tolerances, we make heat shields that go on steering thruster engines for satellites by electroforming in nickel. These are extremely light weight with gold interiors to reflect the thermal energy.

Heat Exchangers
Heat exchangers for all sorts of applications, including rocket engines, can be made by machining grooves into a base metal, filling the grooves with wax, electroforming copper or nickel over the wax, bonding it to the base metal, then removing the wax leaving intricate channels throughout the structure. This makes a heat exchanger of any size or shape with complex cooling channels all of a single piece of metal with no braze or weld joints.
Plastic Injection Molds
Many plastic items to be injection molded require surface detail that cannot be machined, such as golf club grips that look like wrapped leather. We electroform nickel on master images supplied by customers, machine the outsides to fit in their molding machines and remove the master images.

Roto Molds
Many plastic items, such as doll heads and automobile arm rests, are made by roto-molding, where uncured liquid plastic such as PVC is put into a hollow mold which rotates in an oven curing the liquid as it sloshes around, forming a hollow plastic part with features exactly replicating the interior of the mold. Electroforming a master image in nickel and mounting it to a holding structure to go into a roto oven will result in parts that are direct replications of the master image made. We make roto-molds for all sorts of things from Holywood props, casino gambling machine decorations to medical dummies.

Decorative Images and Reproductions
The A.J. Tuck Company made its début as a lamp manufacturer a hundred years ago, making beautiful decorative lamp bases of electroformed copper. We can make a reproduction of any image provided by making a silicone rubber reverse mold from that image, and then electroforming onto the rubber exactly replicating what was provided. Some images we have done are shown in this photo.

Duct Work
Precision metal duct work used to funnel air around jet engines can be made by electroforming nickel. The picture is an example of an electroformed duct that we electroformed. We can make any shape and size as single parts without any seams, for any application. We have made tiny ducts with nozzles for high speed printing of numbers on soda cans as well.
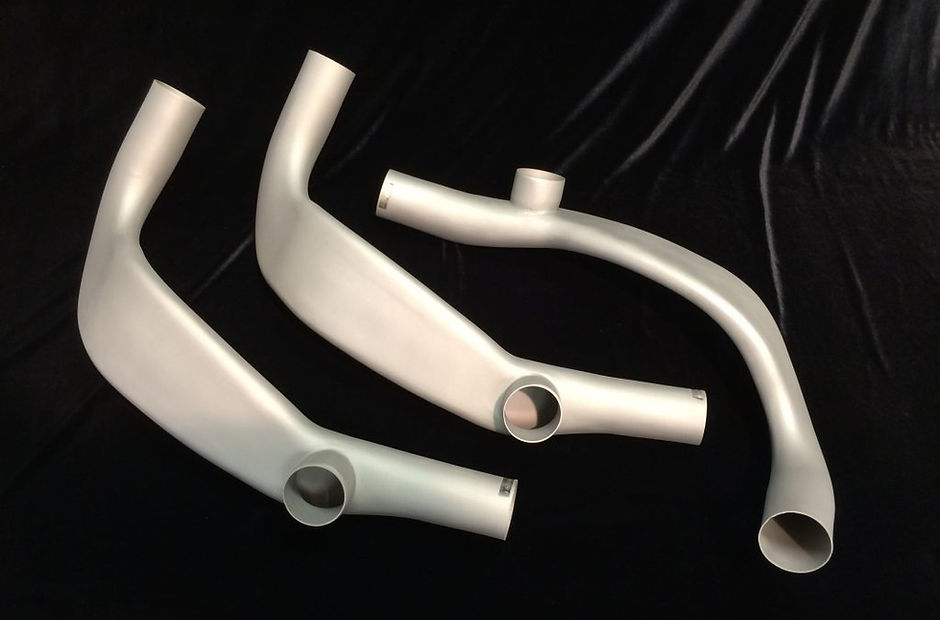
Comparator Gauges
Electroformed comparator gauges are used to determine surface finishes for all sorts of manufacturing processes, such as machining, grit blasting, etc., and can be made by simply electroforming nickel against the actual surface sample, then using that electroform as a mandrel to replicate the surface. We make flat visual gauges that replicate imperfections found on jet engine turbo vanes when the engines are being re-built. We make these by electroforming nickel against the actual defects cut from blades sent to us by the jet engine companies. The technicians see these images on the gauges we make and written instructions tell them what to repair.

EDM Electrodes
Copper EDM electrodes having intricate detail can be made by electroforming in copper. This picture shows an EDM electrode used for cutting an egg crate mold into hard steel.

Medical Hardware
For titanium clip applicators used in laparoscopic surgery, we use our hard nickel to make nickel belts that hold the titanium clips that are fed around and into an anvil pinching them off and sealing off internal vessels without stitching.
