(203) 775-1234
What is Electroforming?
Electroforming is a highly specialized process for fabricating metal parts by electrodeposition in a plating bath over a base form called a mandrel, which is subsequently removed leaving just the electrodeposited metal. The mandrel is fabricated by conventional means and then electroplated. Once the desired thickness is achieved, anywhere between .001″ (.025 mm) up to over a half inch (12.7 mm), the mandrel is extracted or dissolved.

Electroforming was invented in 1838 by a German engineer living and working in Russia, Moritz Hermann von Jacobi. While working on big electric motors and batteries to run them, he developed electroforming, then called galvanoplastics or electrotyping, to make printing plates. Electrotyping has been used ever since to make printing plates in printing factories around the world. One of the most common is the US Mint, making printing plates for dollar bills. Before the turn of the century, the English and the Germans did a lot of galvanoplastics to make all kinds of decorative objects, statues, lamp posts and reproductions of museum artifacts. The Germans had a big electroforming factory before WWII. Read about Moritz von Jacobi here: https://en.wikipedia.org/wiki/Electrotyping
This diagram shows the positively charged electroforming metal source (anode) at the left being broken down by DC electric current causing each surface atom to lose two electrons (ionized) in the copper or nickel electrolyte solution, which are then attracted to the negatively charged mandrel (cathode) where they get their electrons back and become metal again.
The advantage of this process is that metal is deposited on the mandrel surface, atom by atom, reproducing the form of the mandrel exactly, to within less than a micron. Complex features, close dimensional tolerances, and surface finishes can be created on inside surfaces that are impossible to obtain by any other method known.
Electroforming should be thought of as a basic manufacturing process when considering alternatives best suited for making any particular item. Other basic metal forming processes, including casting, forging, stamping, deep drawing, machining, EDM and rapid prototyping may serve well for most applications, but can be pressed beyond their limits when requirements call for extreme tolerances, complexity, or thin walls translating into light weight. Electroforming is the most accurate way of establishing internal dimensions and reproducing surface detail.

Why Electroforming?
Because the metal is formed on a molecular level over a surface, replicating the image needed in reverse, deep and complicated features can be made which simply cannot be produced as internal features without electroforming. Since the metal goes on at room temperature, there is no shrinkage or distortion, leaving internal dimensions of a complex structure having exactly the same finish, detail, and dimensions that were established on the designed and fabricated outside of the mandrel. Electroforming is the most accurate way in the world to make internal cavities or reproduce surface detail. The picture shows a complex featured microwave waveguide next to a mandrel like the one it was made on, and a reflector next to its mandrel.

Internal Dimensioned Parts:
Think of a part with a large length to width/height aspect ratio which possesses complex internal structure needing tight tolerances. If the negative space within the part (what we call the mandrel) was machined, say out of aluminum, what tolerances could be reasonably held? Probably down to ±.0002″ or ±.005 mm. Now lets imagine metal was electrodeposited on the mandrel and then only the mandrel was dissolved away. The remaining electrodeposited metal will possess the same complex dimensions, features, and tight tolerances that the mandrel was machined to, but now as the desired internal geometry. Electroforming is the easiest way to make internal cavities like this, and more accurate than machining, casting, stamping, extruding, dip brazing, or 3D printing.

Surface Detail and Finish:
In the old days, when music was predominantly purchased as vinyl phonograph records, the original was carved with a needle on a plastic disc in the studio, and then nickel was electroformed on the same record to make a metal master. The master was then electroformed to make a mother, which was electroformed multiple times to make stampers. The stampers were then used to stamp the millions of records sold, and no fidelity detail was lost from the initial recording in the studio through all of the replications. The purchased record was played and sounded just like you were in the studio listening to your favorite musician. Surface detail can be replicated down to a molecular level, much smaller than anything you can actually make with conventional manufacturing processes.
If the mandrel is made out of something extremely smooth and shiny, out of something re-usable such as stainless steel, then the electroform will have the exact finish as the mandrel. This is how reflectors are made.
Dollar bills are made using electroformed stampers, made from the artist’s single original engraving. How many stampers do you suppose the US mint needs from that one engraving?
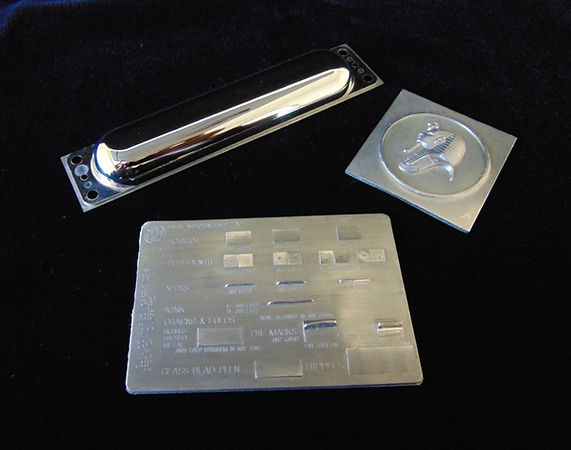
Light Weight Structures:
Suppose you need a thin metal structure having really complex geometry that simply cannot be stamped or machined. We can manufacture an aluminum mandrel having as close tolerances as can be achieved by machining, EDM, etc., electroform a thin layer of metal on that, dissolve the mandrel away, and there you have it - a super lightweight structure with really tight tolerances, better than can be made any other way. In this picture are light weight satellite steering rocket nozzle heat shields and a light weight satellite microwave antenna horn.
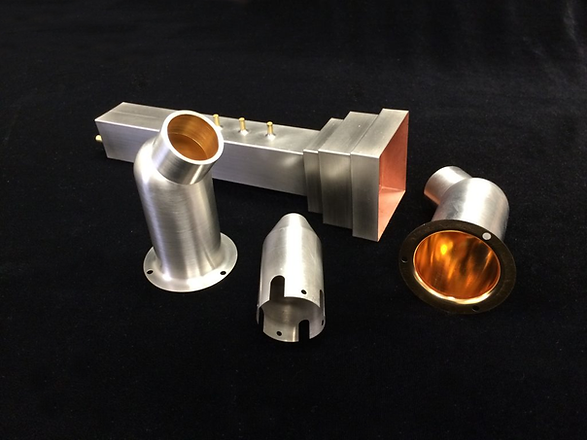
What can we Electroform?
We can make parts of copper or nickel, 4 types of copper, our OFC, Type 1A, Type II and Type IIA, plus 2 types of nickel, our Type 1 and Type II per the chart. We can alter the physical properties of the metals resulting in copper parts ranging from pure soft OFC up to type IIA having 120,000 lbs. / sq. inch tensile strength, and nickel from pure up to Type II having 200,000 lbs. / sq. inch tensile strength with a hardness of Rockwell C-50. Multiple layers of the same or different electroformed metals can be molecularly bonded together, or to different substrate metals to produce complex structures with other “grown on items” such as flanges, baffles, bosses, and inserts.
Sometimes customers need parts of copper that also have high tensile strengths, such as microwave components for satellites. We have repaired high strength copper parts using our Type IIA copper, where we molecularly bond our copper on to the existing part at room temperature and build up just the area that needs repair. This works well as welding would soften the copper, and our bonding is even stronger than welding. We have our own tensile testing equipment and can provide customers with the physical properties of their parts.
Our Rockwell C-50 nickel is very wear and abrasion resistant, while maintaining good ductility. It is good for the inside layer of injection molds, for abrasion resistant applications and for making items that need to survive a lot of handling. We have our own hardness tester and can provide hardness results.
What can mandrels be made of?
Mandrels can be made of a wide variety of materials including stainless steel, aluminum, rubber, epoxy, plastic, plaster, wax, glass, and lithography to name a few. Mandrels that are not conductive can be coated with thin layer of conductive material prior to electroforming. Reusable mandrels can be made of stainless steel or rubber (RTV). Reusable mandrels are only good for parts with no undercuts, otherwise the mandrels need to be disposable, of which the most common material is aluminum. Aluminum can be machined, EDM, etc. to accurate tolerances and after electroforming, can be removed in a process which does not damage or etch the copper or nickel.
